压片模具在制药、化工、食品等行业中广泛应用,是生产线上的重要一环。然而,随着使用时间的增长,模具不可避免地会出现各种故障。
一、常见故障及其原因
压片不均匀:这可能是由于模具的上下模之间的间隙不均匀,或者模具本身存在磨损、变形等问题。
压片厚度不达标:这通常与模具的调整不当、压力不足或材料本身的质量有关。
模具卡死:可能是由于模具内部有异物、润滑不足或材料填充不均匀导致。
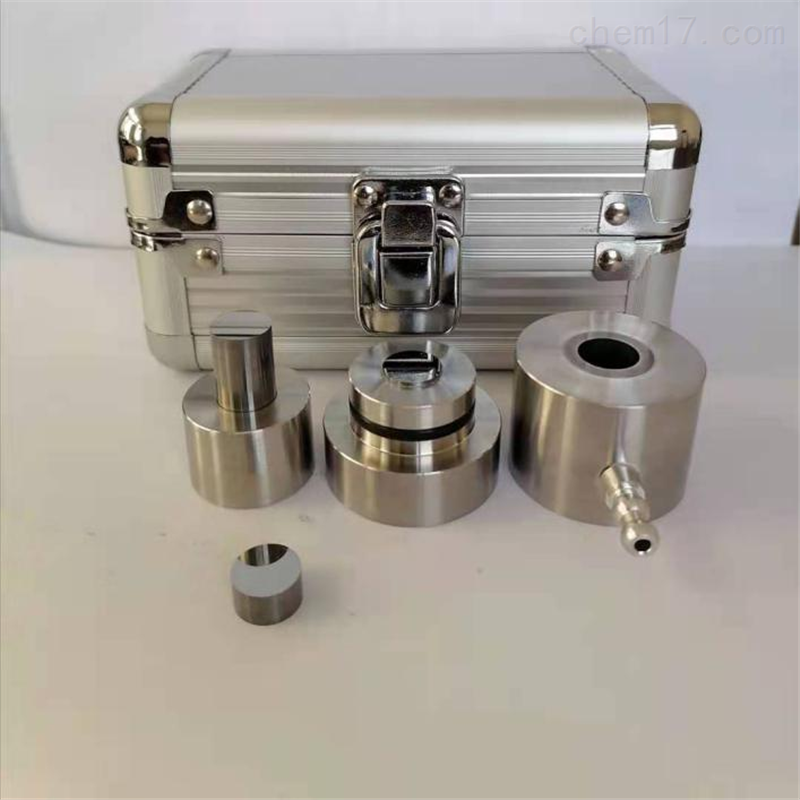
二、故障排除步骤
观察与诊断:首先,操作人员应仔细观察模具的工作状态,注意压片的质量、厚度以及模具的动作是否顺畅。通过初步观察,可以大致判断故障的类型和原因。
检查与调整:根据初步诊断,操作人员应对模具进行详细检查,包括模具的间隙、磨损情况、润滑状况等。在检查过程中,可以对模具进行适当的调整,如调整间隙、更换磨损部件等。
清洁与润滑:对于因异物或润滑不足导致的故障,操作人员应定期清洁模具内部,并添加适量的润滑剂,以保证模具的正常运行。
维修前的准备:在进行模具维修前,操作人员应确保工作区域的安全,准备好所需的维修工具和备件。
拆卸与检查:根据故障类型和维修需求,操作人员应正确拆卸模具,并对其进行仔细检查。在拆卸过程中,应注意保护模具的各个部件,避免损坏。
更换与修复:对于磨损严重或损坏的部件,应及时更换。在更换过程中,应确保新部件的规格、型号与原部件相符。对于可修复的部件,如轻微的磨损或变形,可以采用修复方法进行处理。
组装与调试:在更换或修复完部件后,操作人员应按照正确的顺序重新组装模具。组装完成后,应对模具进行调试,确保其工作正常、压片质量符合要求。
四、压片模具的日常保养与维护
除了故障排除和维修外,日常保养与维护也是确保模具正常运行的关键。操作人员应定期对模具进行清洁、润滑和检查,及时发现并处理潜在问题。同时,还应建立模具的使用记录和维护档案,以便更好地掌握模具的使用情况和维护历史。